การกำจัดหรือการลดโปรตีนในน้ำยางธรรมชาติ
การกำจัดหรือการลดโปรตีนในน้ำยางธรรมชาติ (deproteinisation) เพื่อป้องกันอาการแพ้แบบ type-I และเพื่อให้ได้ผลิตภัณฑ์ยางที่มีระดับของโปรตีนต่ำ สามารถทำโดยใช้วิธีกล เช่น การเหวี่ยงหมุนหลายครั้ง (multi centrifuging) หรือการแยกด้วยเมมเบรน (membrane filtration) วิธีเคมี เช่น การย่อยโปรตีนด้วย proteolytic enzyme หรือการใช้สารลดแรงตึงผิวแล้วตามด้วยการทำให้บริสุทธิ์โดยการใช้เครื่องหมุนเหวี่ยงให้ตกตะกอนหรือส่วนที่หนักกว่านอนก้น (centrifugation) หรือการทำให้น้ำยางเป็นเนื้อครีม (creaming)โดยสามารถใช้ centrifugation ร่วมกับ creaming ได้ (George, KM., et al., 2007)
1. วิธีเคมี Vystar ได้พัฒนาเทคโนโลยีเพื่อกำจัดโปรตีนที่ทำให้เกิดอาการแพ้ (allergenic protein : AP) โดยการใช้สารเคมีอะลูมิเนียมไฮดรอกไซด์ (aluminium hydroxide: Al(OH)3) และซิลิกาไดออกไซด์ (silica dioxide : SiO2) ทำปฏิกิริยากับน้ำยางก่อนเข้าสู่กระบวนการวัลคาไนเซชัน (vulcanization) ซึ่งสามารถทำให้ระดับของ AP ลดลงน้อยกว่า 0.2 g/g (Honeycutt, T., et al., 2006) ซึ่งสารเคมีที่ใช้เติมนั้นแบ่งเป็น 5 ชนิด คือ
1.1 Inorganic salts ได้แก่ อะลูมินัมคลอไรด์ (aluminum chloride: AlCl
3) อะลูมินัมซัลเฟต(aluminum sulfate: Al
2(SO
4)
3) แมกนีเซียมคลอไรด์ (magnesium chloride: MgCl
2) ซิลเวอร์ไนเตรต (silver
nitrate : AgNO
3) และซิงค์ไอโอไดด์ (zinc iodide : ZnI
2) โดยเกลือเหล่านี้สามารถละลายได้ในน้ำกลั่น
1.2 Inorganic oxides และ Inorganic hydroxide ได้แก่ อะลูมินัมไฮดรอกไซด์ (aluminum hydroxide : Al(OH) 3) ไททาเนียมไดออกไซด์ (titanium dioxide : TiO2) ฟูมซิลิกา (fumed silica) และซีโอไลต์ (zeolyte) เนื่องจากสารประกอบนี้ไม่ละลายน้ำ จึงใช้เติมลงใน 45-50% โซเดียมไฮดรอกไซด์ (NaOH) หรือ โพแทสเซียมไฮดรอกไซด์ (KOH) ก่อน ส่วน TiO2 ปกติจะละลายในด่าง โดยจะเติมลงใน NaOH 50%
1.3 Metal powder ได้แก่ อะลูมินัม (aluminum :Al) ซิลเวอร์ (silver : Ag) และอะลูมินัมไวร์ (aluminum wire : Al-wire) ที่อยู่ในรูปของแป้ง สามารถใช้เติมในน้ำยางธรรมชาติได้โดยตรง
1.4 Organic compounds ได้แก่ ฟอร์มาลดีไฮด์ (formaldehyde) เกลือโซเดียมของเบนซีนซัลโฟนิก (sodium salt of benzenesulfonic) และกรดเบนซีนซัลโฟนิก (benzenesulfinic acids) โซเดียมดีซิลซัลเฟต (sodium decylsulfate) อะคริลลาไมด์ (acrylamide) ซิงค์กลูโคเนต (zinc gluconate) ซิงค์อะซิเตต (zinc acetate) และคอปเปอร์อะซิเตต (copper acetate) ที่สามารถเติมในน้ำยางได้ทั้งในรูปของของเหลว สารละลายหรือของแข็ง
1.5 Polymeric absorbents ได้แก่ Lupamin 9010, Lupamin 1595 (BASF), Lupasol FG, lupasol G20 (BASF) และ lignins (Honeycutt. T., et al., 2007)
Vystar เตรียมสารเคมีที่ใช้กำจัดสาร allergens คือ Al(OH)3 (Al2O3 57%) และ SiO2 ( fumed silica 99.8% ขนาด 0.011 ไมครอน) โดยนำมาละลายใน KOH (ความเข้มข้น 50%) และผสมกับน้ำยางธรรมชาติที่อุณหภูมิห้อง แล้วกวนให้เข้ากันนาน 24 ชั่วโมง (สำหรับ SiO2) และ 72 ชั่วโมง (สำหรับ Al(OH)3) การทำปฏิกิริยาระหว่างน้ำยางธรรมชาติและส่วนผสมของสารเคมีดังกล่าวจะทำให้ความทนทานต่ออายุการใช้งาน (aging resistance) ดีขึ้น การที่น้ำยางธรรมชาติทำปฏิกิริยากับ SiO2 จะลด break point ลง แต่ก็เพิ่มความเสถียร (stability) และการย่อยสลาย (degradation) รวมทั้งความทนทานต่อแรงดึงและการยืดตัวจนขาดของยาง (Honeycutt, T., et al., 2006)
2. การใช้เอนไซม์ (enzyme treatment) การใช้เอนไซม์ช่วยย่อยสลายโปรตีนในน้ำยางธรรมชาตินั้น เป็นวิธีที่มีประสิทธิภาพมาก เนื่องจากช่วยรักษาคุณสมบัติเดิมทางกายภาพและสมรรถภาพของยางธรรมชาติ ปกติยางธรรมชาติจะมีโปรตีนเป็นส่วนประกอบประมาณ 2% โดยน้ำหนัก สามารถละลายได้ในน้ำและอยู่ในรูปของสารสกัดโปรตีน (extracted protein) ในกระบวนการผลิตถุงมือยางที่ใช้ทางการแพทย์นั้น โปรตีนจะย้ายไปอยู่ที่ผิวหน้าของถุงมือยางขณะอบแห้ง (drying) และการขึ้นรูปยางโดยใช้ความร้อน (heat vulcanization) ทั้งนี้การชะล้างด้วยน้ำ (water leaching) สามารถกำจัดโปรตีนออกจากผิวหน้าได้ แต่ไม่สามารถกำจัดออกได้หมด ซึ่งเอนไซม์ที่ใช้ ได้แก่ Proteases เป็น hydrolytic enzyme ที่สามารถทำให้พันธะเพปไทด์เกิดการแยกออกได้ ซึ่งการใช้เอนไซม์ย่อยโปรตีนในน้ำยางเป็นวิธีที่นิยมใช้ในอุตสาหกรรม เอนไซม์นี้ได้จากการหมักแบคทีเรียสายพันธ์ที่ไม่ก่อให้เกิดโรค (nonpathogenic strain bacteria) โดยใช้ในรูปของผงหรือสารละลาย ในปี 1998 บริษัท Tillotson Healthcare Corporation ได้ร่วมมือกับบริษัท Allox, LLC ใช้เอนไซม์ย่อยโปรตีนในน้ำยางและพบว่าสามารถลด allergenic protein ได้สูงถึง 95% (จากการทดสอบด้วยวิธี ELISAs และ RASTs Test) (Perrella, FW., and Gaspari, AA., 2002) นอกจากนี้ยังมีเอนไซม์ papain ที่สามารถย่อยสลายโปรตีนได้ ซึ่งผลิตจากมะละกอ (Carica papaya) โดยพบว่าถุงมือยางที่ใช้เอนไซม์ papain ย่อยสลายโปรตีนนี้สามารถลดปริมาณโปรตีนที่เหลืออยู่ในถุงมือยางได้น้อยกว่า 50 µg/dm2 (George, KM., et al., 2007) นอกจากนี้ยังพบว่าการใช้เอนไซม์ร่วมกับการล้างด้วยสารลดแรงตึงผิวมีประสิทธิภาพเป็นอย่างมากในการเตรียมน้ำยางธรรมชาติที่มีความบริสุทธิ์สูง (Ichikawa, N., Hwee, EA., and Tanaka, Y., 1993)
การใช้เอนไซม์ช่วยย่อยสลายโปรตีนในน้ำยางธรรมชาติทำโดยการใช้ alkaline proteases 0.025% ทำปฏิกิริยากับน้ำยางธรรมชาติชนิดแอมโมเนียที่ผ่านการเหวี่ยงหมุน (centrifugated ammoniated natural rubber latex) ที่อุณหภูมิ 13-32 องศาเซลเซียส นาน 1-2 วัน จากนั้นเอนไซม์และน้ำยางที่ได้ทำปฏิกิริยากัน (enzyme-treated natural rubber latex : ET-NRL) จะถูกนำไปแช่แข็ง ทำให้ละลายและเหวี่ยงหมุนเพื่อแยก โปรตีนที่สกัด (extracted protein) ออกมา การหาปริมาณโปรตีนที่เหลืออยู่ในถุงมือยางภายหลังกระบวนการผลิตนั้นจะนำโปรตีนมาสกัดด้วยสารละลายที่มีค่าความเป็นกรด-ด่าง (pH) 7.4 นาน 2 ชั่วโมง โดยใช้การทดสอบ 3 วิธี คือมาตรฐาน ASTM D5712 Lowry เพื่อหาปริมาณโปรตีนทั้งหมด ELISA เพื่อหา allergenic protein ในน้ำยางธรรมชาติ และ RAST inhibition เพื่อหาสาร allergens ที่เป็นปัญหาของผู้ที่ใช้งาน ผลที่ได้แสดงในตารางที่ 1 (Perrella, FW., and Gaspari, AA., 2002)
3. การใช้สารลดแรงตึงผิว (surfactant treatment) สารลดแรงตึงผิวชนิด non-ionic surfactant สามารถลดสาร allergens ได้มากกว่า 95% ซึ่งสารลดแรงตึงผิวที่นิยมใช้คือ TritonTM X-100 และโซเดียมโดดิซิลซัลเฟต (sodium dodecyl sulfate : SDS) การใช้ TritonTM X-100 ควบคู่ไปกับการล้าง 4-5 ขั้นตอน (alginate creaming-phase separation - redilution) จะลดสาร allergens ได้มากถึง 98-99% (Schloman, JR, WW., Teetor, VH., and Ray, DT., 2006) รูปที่ 1 เป็นการเปรียบเทียบขั้นตอนในการลดสาร allergens ที่ชี้ให้เห็นว่าการใช้สารลดแรงตึงผิวทำให้ปริมาณสาร allergens ลดลงเป็นอย่างมาก (ทั้ง TritonTM X-100 และ SDS) แต่การใช้สารลดแรงตึงผิวก็มีข้อเสียคือ ทำให้ประสิทธิภาพในการวัลคาไนเซชันลดลง โดยดูจากค่า crosslink density (รูปที่ 2) ซึ่งตรงข้ามกับน้ำยางธรรมชาติที่ไม่ผ่านการล้าง (unwashed latex)
ตารางที่ 1 แสดงปริมาณโปรตีนที่ก่อให้เกิดอาการแพ้ที่เหลืออยู่ในถุงมือยางและน้ำยางธรรมชาติ
Test methods
|
RAST
|
ELISA
(mg/g)
|
Lowry
(mg/g)
|
(mg/mL)
|
(mg/g)
|
Samples
|
NRL
|
Gloves
|
Gloves
|
Gloves
|
Untreated control (a)
Enzyme treated (b)
Expt 1
Expt 2
% Reduction
(100 ´(b/a))
|
3311.0 ± 680.1
33.0 ± 50.5
(n=5)
-
>99
|
364.6 ± 129.6
13.4 ± 9.8
(n=5)
5.8 ± 3.6
(n=5)
>96
|
211.2 ± 43.9
0.8 ± 0.8
(n=5)
1.0 ± 0.7
(n=5)
>99
|
89.0 ± 30.6
101.6 ± 13.8
(n=5)
-
-14
|
ที่มา : Perrella, FW., and Gaspari, AA. (2002)
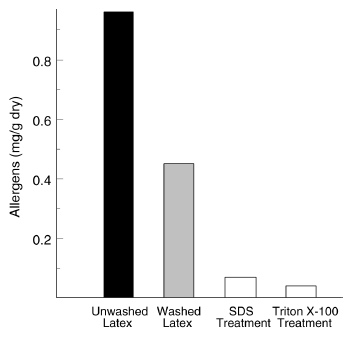
รูปที่ 1 แสดงปริมาณสารก่อให้เกิดภูมิแพ้ (allergens) ในน้ำยางที่ผ่านขั้นตอนต่างๆ
(Schloman, JR, WW., 2002)
รูปที่ 2 แสดงค่า crosslink density ของแผ่นฟิล์มจากน้ำยางที่ผ่านขั้นตอนต่างๆ (Schloman, JR, WW., 2002)
4. การใช้ fumed silica กลไกการลดโปรตีนในน้ำยางธรรมชาติของซิลิกานั้น อาจเนื่องมาจากการรวมตัวของสารประกอบระหว่างโปรตีนและไขมันในน้ำยาง เมื่อเติมแอมโมเนียลงไปเพื่อรักษาความเข้มข้นของน้ำยางแล้วจะทำให้ส่วนที่เป็นไขมันไฮโดรไลซ์อย่างช้าๆ และเกิดกรดไขมัน (fatty acids) ขึ้น ทำให้สามารถดูดซับโปรตีนออกจากอนุภาคของน้ำยางได้ขณะผสมน้ำยางกับสารเคมีเพื่อนำไปขึ้นรูปผลิตภัณฑ์ (compounding) ซึ่งเกิดการแทนที่ของโปรตีนโดยซิลิกาแสดงไว้ในรูปที่ 3 ซิลิกาจะทำหน้าที่เป็น thickening agent และช่วยเพิ่มความแข็งในการฉีกขาด (tear strength) ความเสถียร (stability) ของยาง โดยปริมาณ fumed silica ที่นิยมใช้เพื่อลด extracted protein ออกจากน้ำยางและสาร allergens คือ 1-5% และ 1% โดยน้ำหนัก ตามลำดับ (Amdur, S., 1999) และจากการทดสอบตามมาตรฐาน ASTM D 5712 และ LEAP test, Guthrie Research Institute, Sayre, PA พบว่า ปริมาณ extracted protein และสาร allergens มีค่าน้อยกว่า 28 ppm และน้อยกว่า 0.2 ppm ตามลำดับ นอกจากนี้ยังสามารถควบคุมการไหลของยาง (rheology) รวมทั้งยังช่วยปรับปรุงคุณสมบัติอื่นๆ เช่น ความทนทานต่อแรงดึง (tensile) และความทนทานต่อการสึกหรอ (abrasion resistance) ของยาง เนื่องจากอนุภาคของ fumed silica มีความละเอียดจึงทำให้แผ่นฟิล์มยางที่ผลิตขึ้นมีลักษณะโปร่งแสง (translucent) (Conn, R., et al., 2008)